Ryan Schulok
Mechanical Option
Pharm Corporation
-Pills, DE-
Technical Report 1 discusses compliance of Pharm Corp. with ASHRAE 62.1 and ASHRAE 90.1.
TECHNICAL REPORT 1
Technical Report 1 discusses compliance of Pharm Corp. with ASHRAE 62.1 and ASHRAE 90.1.
Technical Report 1 documents the compliance of Pharm Corp. with respect to ASHRAE 62.1-2010 Ventilation for Acceptable Indoor Air Quality and ASHRAE 90.1-2010 Energy Standard for Buildings Except Low-Rise Residential Buildings. The primary use of this building is serving as the headquarters for Pharm Corp. providing office and conference space for employees.
​
The first part of this report discusses ASHRAE 62.1-2010 Section 5 and Section 6. Section 5 discusses systems and equipment that are used within the building, how the systems are controlled, varying HVAC equipment as a function of internal loads, and removal of contaminants within the building. It also comments on restrictions of thermal envelope U-values that may be used.
​
Section 6 discusses ventilation breathing zone procedures, ensuring that each zone is receiving at least the minimal required outdoor air. Appendix B, within the report, visually shows the breathing zone air flows that were calculated per zone. Pharm Corp. is in compliance with Section 6, maintaining the minimal outdoor air intake to be greater than the maximum exhaust air.
​
Most cases per ASHRAE were exceeded by more than the minimal amount, due to the required installation of state-of-the-art energy efficient equipment and lighting. These are seen in ASHRAE 90.1. Although this building is not LEED certified, much of the equipment installed and design energy use succeeds to comply to LEED.
​
​
​
Technical Report 2 analyzes the energy consumed by the building and plant annually for Pharm Corp, located in Delaware. The information from this report was gathered from the mechanical and architectural drawings provided by both AKF Group, and Granum A/I.
​
With the use of Trane Trace 700, the building was modeled and analyzed for energy consumption, peak design load and operating cost throughout a year. All of the assumptions and schedules were either provided by AKF Group, such as occupancy and ventilation rates, or based on general office operating schedules selected in Trane Trace 700. ASHRAE 62.1 was used for ventilation rates. ASHRAE 90.1 was used for lighting power density values through office space, atrium space and dining areas.
​
The cooling plant modeled is a closed-circuit cooling tower providing condensate to a water-cooled DX AHU. Heating is provided by the air-side economizer at the unit, with additional electric reheat coils in the VAV terminal unit boxes. Perimeter heating is at all the curtain walls and windows.
​
The cooling load calculated by Trane Trace 700 is 627.4 SF/ton compared to the design documents value of 505.2 SF/ton. The cooling load has a relationship with electric demand, along with the temperature fluctuation. Both cooling and electric demand increase as a function of temperature, as found from Trane Trace.
​
Heating loads are low, being 9.0 BTUh/SF from Trace and 7.9 BTUh/SF from the design documents. Minimal values are concluded to be due to economizer usage, along with possible overestimation of lighting and equipment loads. Outdoor air ventilation in Trane Trace is 14%, which was the designed outdoor air intake for the mechanical equipment in the design documents.
​
Mechanical energy consumption within the building, from Trace, was 19% for Heating Plant, 32% for Cooling, 28% for Lighting and 11% for both Fans and Receptacles. The entire cost for the mechanical system, including maintenance, electricity and water, the total operating cost is $1.70/SF. The overall electric load demand of 1.7 kWh creates the byproduct CO2 of over 2.7 million lb/year.
​
​
​
​
Technical Report 3 is the third of three technical reports in evaluating Pharm Corp. This technical report is discussing the existing conditions of the mechanical systems. From the design requirements of indoor and outdoor conditions, it was determined that all airhandling units and rooftop units supply more than the required ventilation air. The estimated heating and cooling loads calculated in Trane Trace 700 underestimate the cooling loads from the design documents.
​
Energy consumption within the building was determined to be 67% electricity of total energy cost, 29% of energy cost is from water, and the remaining energy costs is the maintenance to operate the building. A total of 1.7 million kWh and 2.1 million gallons of condenser water are required for this building it operate annually. Electricity consumption is rather constant throughout the months, peaking toward December and January, while condenser water tends to peak in the summer months and decay in the winter months.
​
Mechanical systems are divided into indoor air units, outdoor air units and condenser water schematics. The cooling towers provide condenser water to condenser pumps, which is sent to water cooled DX air-handlers. As for the outside system, RTUs send air to a dedicated conference room with demand control, which contributes to LEED credits. However, this credit cannot be received due to the rest of the building lacks demand response. The overall building did not receive any LEED credentials when the LEED-NC evaluation was conducted.
​
With system first costs being undisclosed due to the owner’s request, the upfront cost is unknown. The rebates that can be awarded for this site, however, are crucial. It was determined that if this site used solar photovoltaics, the site can receive a $240/kWh that is created by the solar PV system. Electricity costs were determined, based on arbitrary values of 1% of total electricity generated by the PV system, the rebates can total to over $4 million dollars for each of the first 10 years.
​
Possible avenues to investigate based on this report are the reduction in mechanical space that is taken up on each floor by moving units to the roof, introducing a chiller that can control an active chilled beam system which will greatly reduce the mechanical room size, and reducing the electricity consumption that the mechanical system consumes, primarily for heating. Installation of a boiler, with a chosen fuel for low emissions and high efficiency, will increase the cost of the heating system up front, but will greatly reduce the electric consumption responsible for heating. Enacting one or more of these possibilities may contribute to LEED accreditation, which can be a feasible goal if funds, life-cycle costs, and payback period are acceptable.
​
​
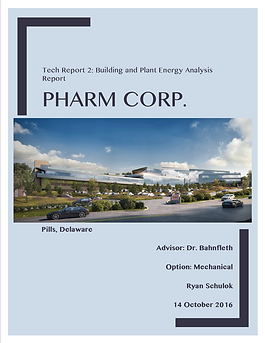
Technical Report 2 analyzes the building and plant energy consumption throughout the building.
TECHNICAL REPORT 2
Technical Report 3 analyzes the existing mechanical systems designed for the building, and LEED evaluation for the building.